“I have a 10.8 HP motor that can get up to 3600 RPM. I am running a large sprocket that’s 54 teeth on a live axel and a small sprocket that’s 12 teeth on a jackshaft that has a heavy duty torque converter.
I currently have a #40 chain on it and it breaks and/or falls off. What is the problem?”
The first and primary cause for the chain coming off is chain elongation. This is a common problem with go karts, especially the chain falling off because of elongation. What occurs when the go kart has been used for a while the chain elongates (becomes longer) and the slack between the chain and the driver becomes excessive. The result is that the chain will come off if the gap is not adjusted.
The second problem is that the chain may not be matched up with the engine/go kart properly and therefore the chain elongates excessively fast and even in this case, breaks.
If a chain keeps breaking, the problem is that the chain cannot handle the load.
So the diagnosis of the system is needed to determine what horsepower is going through the chain.
Part of the equation here is that the unknowns are not fully understood. When I say unknowns I am referring to the parts that contribute to the system. In this case they are the following:
-Engine Horsepower
-Torque-averter Input/Output Torque
-Jack Shaft Drive Input/Output Torque
-Tire Size
-Weight of the Go Kart-
-Weight of the person in the Go Kart-
-Chain Type
-Chain-Tensioner System
The customer has given the important information at the outset, but we are missing some information on the torque-averter and the weights (gokart-driver).
It is important to have the weight and all the gear ratios for a good assessment of the drive system. Bottom line is that the go kart is a mass and it is being propelled about by a motor. This mass is essential for a good drive line evaluation.
Additionally, any component in the drive line, whether it is a gear box, a jack shaft or a torque-averter has an overall input/output ratio and that contributes to the performance of the go kart.
After doing some digging the following information was given:
-400 lb go kart
-250 lb person
-Schematic for the torque-averter.
Analysis of the Torque-Averter
The following schematic was given. Trouble is that no other information was given. The assumption here is that the schematic is essentially to scale, or very close to scale. So the picture was measured (using scaling principles) and the diameters of the pulleys was derived from these measurements.
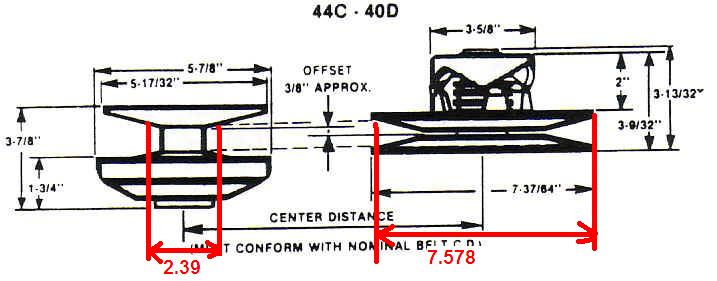
The Torque-Averter in its optimum configuiration for maximum torque has the driver end at the smallest possible position, the driver end at the largest position. The set up position, as shown here (off of the Comet Clutch manual document) is the optimum position. The diameters were approximated using scaling.
The small pulley was measured to be 2.39 inches in diameter. The larger pulley was 7.57 inches. The overall ratio of the system is 7.57/2.39 equal 3.17/1
The following diagram was developed:
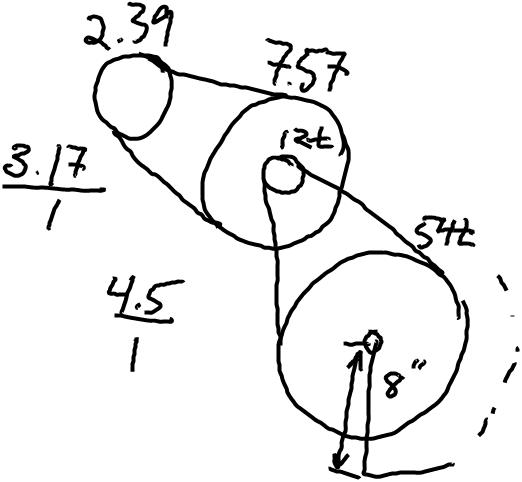
Torque Averter free body diagram for the over all drive train
Here is a handy calculation in case you have forgotten how to figure out the diameter of a drives sprocket:
Radius Drive Sprocket = Pitch/Sin(360/Number of Teeth)
The pitch of the chain is a #40 = .50 inches
Plugging the tooth values into the equation above we come up with:
54 tooth sprocket = 4.3 inch radius
12 tooth sprocket = 1 inch radius
What we are trying to achieve is the tension in the chain, which is in the second drive line system. So first we need to calculate the torque from the engine and out of the torque-averter system.
We know that the ratio for the torque-averter is 3.17/1 and that the engine torque is 189 in-lbs.
The output torque for the torque-averter is 189*3.17 = 599.13 in-lbs
So the torque that the 12 tooth sprocket is developing is approximately 600 in-lbs.
The chain wraps on this sprocket and then transfers tension to the larger sprocket. The chain tension is therefore a force multiplied times a radius to get the equivalent torque.
Torque = Tension * 12 tooth sprocket radius
The unknown is the tension:
Manipulate the equation:
Tension = Torque/12 tooth sprocket radius
In this case the 12 tooth sprocket radius = 1 inch making the math easy. The tension is 600 lbs.
For a closer evaluation, we have a go kart that is probably accelerating a lot and is using the full horsepower for about 50% of the time the go kart is being operated.
We have merely calculated the tension so that we can evaluate the chain.
If we are designing a go kart the next step would be to calculate how well the go kart is going to perform. The reason for this is that we will be chasing our tails and doing a lot of rework if we have no idea how well the go kart is going to perform.
Because the Engineering Tool Kit program does not have a Jack Shaft calculator in it, we are going to assume that the torque-averter/drive system are one whole unit, or it is a single/clutch driver and single driven axel.
As far as the program is concerned, all it cares about for go kart performance calculations is an overall ratio.
To determine the overall ratio, the 54tooth/12 tooth = 4.5/1. The overall ratio of the entire system is 4.5/1 (main drive system) *3.17/1 (torque-averter system) = 16.69/1
In the engineering tool kit program we will plug in the following:
400 lbs frame
250 lb person
10.8 hp @ 3600 rpms
12 tooth sprocket
(resulting sprocket for the rear drive = 12 * overall ratio {16.69}) 200.34 tooth rear sprocket
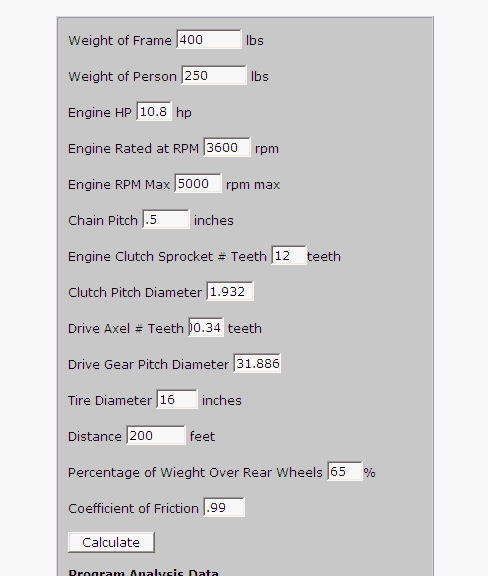
Go Kart Drive Line Variables Input, Weight, Engine Drive Sprocket, Main Drive Sprocket and Tire Diameter. Chain Pitch is .50 or #40 Chain
The result is an acceleration of 5.0 second over a 200 foot span. What this is telling us is that the go kart has a pretty good acceleration, in fact if it were to be compared to a dragster, it would accelerate to 60 mph in about 5.3 seconds. Some of your hotter cars have this kind of acceleration….
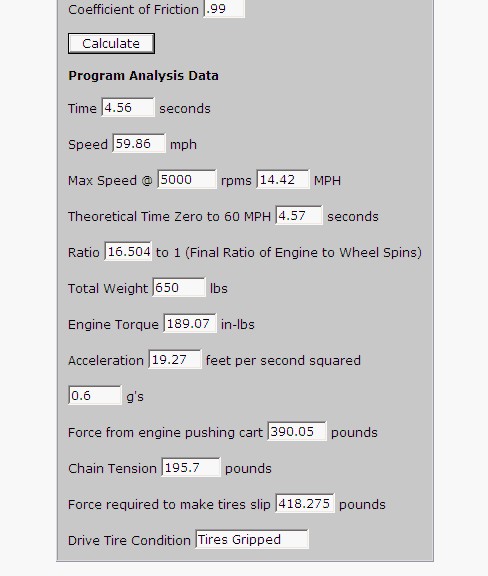
Go Kart Drive Line Program Results. Notice the chain tension is way off, because this program does not do jack shaft calcualtions…yet.
That aside, the performance of the go kart is really okay. In other words, we are probably not smoking clutches because the drive line is a problem.
A word on the over all performance of this go kart. In reality this go kart probably does not accelerate like a madman out of the bat cave because the torque-averter clutch will start to change ratios making the go kart change in ratio. This change in ratio will cause the go kart to not to continue accelerating at the same insane pace.
Now that we have evaluated the drive line and the overall performance of the go kart we need to look at the chain. The complaint initially is that the chain is breaking. So an analysis of the chain is required.
Unfortunately, because the program does not have jack-shafting included, this part of the calculation must be performed by hand (that is until I write he program that includes the jack-shafting!) The program currently includes a chain tension, but this tension is not the correct tension of the chain. The chain tension is as if the system was one big rear sprocket and one small drive clutch sprocket. If you think about it, the drive gear would be way, way too big and would touch the ground leaving the tires high and dry.
But that does not mean we got useless information. You can use this program to double check your work, especially for engine torques, sprockets sizes, overall performance and so on. Bottom line, the basic understanding of torque/forces needs to be comprehended. (Go to the basic drive line calcs and it is also discussed in detail in the 201 book)
In our Go Kart Building 201 course we have a program that you can down load that you can plug the tension into the program. This program is based on other formulas that the ACA (American Chain Association) has set as standards. The output rpm for the torque-averter will be the engine ratio divided by the ratio: 3600/3.17 = 1135 rpm.
Now in the chain selection program, the system requires that you input, the tension, rpm and how many links of chain, or at least the center to center distance between the drive and driven sprockets. Additionally the size of the sprockets will be required as well.
A chain is a series of hinges. As we know from basic hinges they wear out. The pin and the barrel wear into one another, much like a file rubs against steel. The minute or very small wear occurs only one side of the chain barrel and pin. The wear is increased by the following factors:
-Angle of articulation
-Load put on the link
-Speed of the link
-Lubrication
The two largest factors for wear are load and lubrication. In the program they are big on shock load and lubrication.
You will notice that as you play around with no lubrication, the chain selection will be rejected.
One of the things to understand about chain manufacturers is that they are recommending chains that will last for 15000 hours in specific applications. That is equivalent to running steady for 1 ¾ years. Chains are used in power train applications such as conveyors in factories and are expected to last for years not hours.
A go kart is a different animal and typically is not run for years, but for hours. Racing go karts for example will thrash a chain after two or three races for cause. They are pushing the chain to its limits.
What we are dealing with in this particular go kart application is a chain that is being pushed to the limits.
In order for me to get the program to actually accept the parameters of the design, I had to make all things at the optimum, no shocks, indoor running, best lubrication. That was just to get it to accept it. Then it yielded the result of 79 hours of running before the chain would be junk.
The nice thing about the program is that is can recommend a chain based mainly on lubrication and shock loading.
So as the chain became more and more shock loaded the pitch of the chain increased. The worse case recommendation was a #60 (.750) chain and the moderate case was a #50 (.625) chain.
In case the option for having a heavy duty chain is not in the cards, or you do not have access to the larger style chain the strands can be doubled or tripled. So you can run to chains side by side to share the load.
After running the program with two strands of #40 the program said it would easily hold up, even with minimal lubrication.
So in the end there were three options:
-Two strands of #40 chain
-1 Strand #50 chain
-1 Strand # 60 chain
Conclusion:The problem with the application in its current state is that the chain is being overloaded even in optimum design conditions. When you factor in the fact the chain is on a go kart with dusty conditions and poor lubrication, it is not surprising that the chain failed.
Additionally, the chain would come off the sprocket easily because the chain slack was not being taken care of. Careful monitoring of chain slack is a must for a go kart without a chain tensioner. What occurs is that the chain slack turns into a massive centenary that can easily skip track. Catenaries typically skip track with sudden shifts in load and rpm.
A go kart needs good chain slack care other wise the centenary is going to skip repeatedly. In the go kart plans, and is also discussed in the ebooks, the chain tensioner is a handy mechanism for controlling chain dynamics. It also makes engine placement so much easier.
For this particular go kart, I am guessing that a chain tensioner was not used and that would contribute to the chain problems. As noted by the customer, it seemed like he was playing around with the chain a lot. Lack of a chain tensioner and the higher loading would cause this problem.
To correct this a larger chain pitch (coupled with the same sprocket teeth selection) or two strands of #40 chain would be the solution. As always it is ideal to have the chain lubricated, otherwise the chain life will be drastically reduced.
A drip oiler, or even a redirecting of the PVC valve outlet to the chain is ideal, because excess oil comes out of the PVC valve and will get dumped directly on the chain.