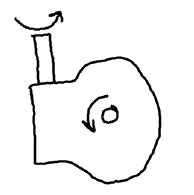
Basic Worm Gear Box from the side
Worm gear drives seem to be the simple solution to the vertical engine problem: a simple driver attached to a worm gear box and a 90° orientation coming of the gearbox and all you have to do is hook up the output shaft to a go kart.
The initial analysis or proposal appears to be very sound, however until you dive in and take a look at the gearbox itself do you realize the issues involved with worm gear drives.
For those not familiar with the worm gear drive let’s break it down. A worm gear drive basically is like a screw that turns on top of a gear on its side. The turning screw moves steadily along and the gear follows the worm profile.
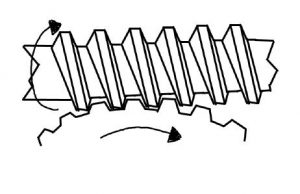
Worm Gear and Main Drive Gear Interface
First of all they are 20% inefficient compared to a planetary gear system. What I mean by 20% inefficient is that friction losses are encountered in the interface between the worm and the main drive gear which are pretty high.
The second problem associated with a worm gear drive is that the amount of work that a worm gear drive can take is limited.
And thirdly the gear ratio required for a go kart is typically substantially different or lower than what a worm to your box delivers. For example he worm gearbox typically will dish out a 20 to 1 ratio whereas a go kart only requires a 10 to 1 ratio.
The fourth problem with a new worm gearbox is the fact that you’re using a screw and it cannot be cross driven easily. What I mean by cross driven is back driven. This can become a problem if the clutch is attached to the input side or screw/worm input of the gearbox. If the go kart needs to coast and the engine is let off the gas you’ll get a sudden jerkingness or hesitance in the drivetrain. This will be the most severe problem encountered with a worm gear drive.
Very often on go carts the best way to slow down the go kart is to use the engine as it is revving down. With the worm gear drive box, because it cannot be back driven you will get a hesitance or a shocky or locked up rear end problem. And this is no light problem either. This can be a very severe out of control problem especially if you’re using it for go carts.
To get a better understanding what a back driving system is doing is, it is trying to force a worm to turn more. In fact you are slamming a gear face against a flat plate and trying to sheer off the worm/screw thread.
The fifth problem is related to the first problem, in that the component sizes must be catered, or designed so that they can transfer heat and stress without wrecking themselves. The main problem that a worm gear drive encounters is viscosity breakdown or high contact worm/gear stress. The main function of oil in a gearbox is to provide a barrier between the metal contacting surfaces and to carry away the heat that is generated during the pressure of event that occurs when two surfaces approach each other with higher force and speed.
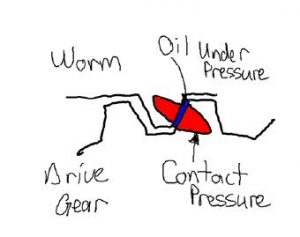
Worm gear contact pressure and oil interface. The oil gets squeezed out at the pressure of the worm gets higher. Shock loads from impacts (such as engine firings) can make the oil film interface brake down. This is also a sliding motion, so the oil is being peeled off the face of the main gear and must be replenished immediatly.
We call this contact pressure, or contact force or even contact points. Worm gear drives require special attention in the worm contact and gear interface points. Additionally adequate oil penetration is required to keep the worm and the gear from actually touching each other. When they do touch each other then you have failure and metal grinding on metal. It is just a matter of time before the worm eats away the face of the gear and the gearbox is rendered useless.
\The speed of the worm is limited to how fast it can go before viscosity breakdown occurs and the oil actually is not helping. As a result the worm gear drive really is not a good fit for engine applications typically.
Typically worm gear drives that are available on the market are designed for fractional horsepower and not for multiple horsepower such as 5 to 10 hp. The reason for this is multiple. First there is not a great demand for gearboxes that require more than half of horsepower, such as a conveyor belt. Secondly the gearbox has the back drive problem which makes it less able to take shock loads such back driving system.
So in short even though it seemed like a good idea to use a worm gear drive on a go kart it is not actually that great an idea after all because of the following issues:
1. Efficiency Is Low
2. Horsepower Capabilities
3. Availability Of Ratios Is Not Applicable To Go Kart Design
4. Cannot Back Drive A Worm Gear
5. Overheating Problems And Ultimate Failure
6. Speed Limitations
7. Overall Packaging Considerations: I.E. Too Heavy And Expensive
The good thing about the worm gears, is that it turns torque into power, which is a good thing.
And i have made a Go Kart with a worm gear in 2001, but since we moved house the kart has not been found
Thanks for the comment;
There are several things to consider when shopping for a gearbox:
1. Is it actually a worm gear, or is it a bevel gear box?
2. How much are you really paying for this gear box? (Free? $20? 100? $200?)
3. In the long term how much abuse can this gear box take before it really breaks down? (10 hours, 100 hours?)
The article that I wrote above was concerning the issues you will encounter when using a worm gear drive. The most noticeable being the back drive problems. The issue is that go karts can vary upon where they are driven. If you are considering driving it in the back woods and never going more than 15-18 mph then a 20:1 gear box may work just fine and you won’t probably notice the back drive problems as much, because you won’t be looking for it.
The problems would be noticed in grass tearing up especially when you let off the gas, or it feels like you are being thrown out of your seat when you let off the gas.
If you size up the gear box sufficiently enough, because most go karts are not driven more than 100 hours in there entire existence, you may never notice the fact that the gear box is ready to take a dump. So it may have appeared to work okay, but in actuality was wearing out and it was not noticeable. Additionally, if the go kart is on the light side (ie 100 pounds or less) you may not be taxing the motor (ie using the horsepower available) and so the gear box may not see the load.
On heavier go karts (170- 250 lbs +) the gear box will see the wear and tear. And if the gear box turns out to be the weak link, you will be mighty upset when you don’t have a replacement.
A word on bevel gear boxes: Bevel gear boxes are available, but again they are kind of pricey ($100- $200). If I were given a choice between a bevel gear box, the vertical engine drive (ie https://gokartguru.com/go_kart_building_202.php) and a worm gear drive, I would select the cheapest option and the most reliable option.
If someone gave me a gear box I would use it until it died.
If I had to lay money down I would put my money in the “vertical engine drive” because it is uses components that everyone has and in the long term is the most versatile as far as speed and torque is concerned. The packaging considerations are actually not any different than that for a gear box.
Regards
The Go Kart Guru
It depends on the quality of the drive. Because I know that many slewing drive or worm drive technologies are used in the wind and solar power industries because of their toughness and ability to have a sustained field life.
In theory it could work, if the drive was specifically designed for the go kart… Probably going to be an expensive investment, so for that reason alone I wouldn’t go that route.
Slewing drives function with standard worm technology, in which the worm on the horizontal shaft acts as the driver for the gear. The rotation of the horizontal screw turns a gear about an axis perpendicular to the screw axis. This combination reduces the speed of the driven member and also multiplies its power; increasing it proportionally as the speed decreases.
The speed ratio of shafts depends upon the relation of the number of threads on the worm to the number of teeth in the worm wheel or gear.
As technology has improved, more and more slewing drives are now functioning with hourglass worm technology which functions much in the same way as a traditional worm with one big exception: a traditional worm touches just one tooth at a time while an hourglass engages up to 11 teeth at one time. This increased tooth engagement results in far greater strength and efficiency.